Docking Station for Autonomous Robot Recharging
|
|
Motivation |
Autonomous mobile robots are being developed to perform
numerous tasks from planetary exploration and mine
sweeping, to entertainment. Each application requires the
robot to survive in its environment, whether it be open or
closed, indoors or outdoors. Operating time is limited for
many of these robots due to their on-board power supplies.
As a result, long-term autonomy is not possible. If this
limitation could be overcome, then mobile robots could be
used for new and more meaningful applications on a regular
basis. In addition, new avenues of mobile robotics research
could be explored. Currently, rechargeable batteries are
typically used that provide power for only a few hours.
Once depleted, the robot/batteries must be connected to a
recharger via human intervention. This results in a
non-continuous robot task cycle as shown in the following
figure, thereby preventing long-term autonomy.
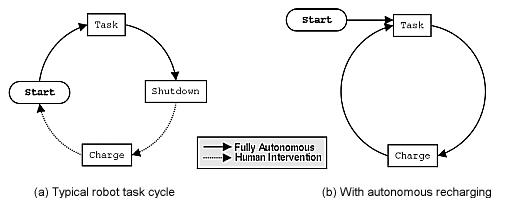
Figure 1: Robot task cycle comparison
|
|
Approach |
A recharging station that allows the Pioneer robot to
recharge autonomously has been developed. The recharging
station physical design is described in two parts: the
docking station and the robot docking mechanism.
|
|
(a) Docking station |
(b) Robot docking mechanism |
Figure 2: Docking station components
|
The docking station is a stationary fixture that provides a
connection point for the robot docking mechanism. A power
charger is connected to the docking station providing the
necessary power. The docking station is designed with 2
passive DOF, providing compliance for numerous robot
docking angles and conditions. The robot docking mechanism
is mounted to the back of a Pioneer robot as shown Figure
5. The robot docking mechanism was designed with one
passive DOF. A contact switch is attached to the robot
docking mechanism, controlling the power connection to the
batteries.
Figure 3: Recharging station setup
Refer to relavant papers and the video clips for more details.
|
|
Experiments |
To test the stability of the docking capability, a robot
was directed to follow a continuous cycle of wandering and
docking for 100 trials. Results of the 100 trials showed a
99% success rate for mechanical docking, and a 97% success
rate for electrical docking. We tracked both mechanical
and electrical docking separately due to the differences
involved to complete each operation.
To test if the robot could survive without human
intervention over an extended period of time, a robot was
programmed as a sentry, monitoring our lab entrance. The
robot wanders while avoiding obstacles until the main doors
of the lab are detected, at which time it stops and begins
monitoring them. Whenever someone opens a door, the robot
takes a picture every second the door is detected open
using a camera. Once the robot's battery voltage level
reached our preset lower limit, the robot began its Docking
Module sequence - looking for the docking station.
Figure 4: Voltage level vs. Time for the monitoring task
Refer to relavant papers for more details.
|
|
Video Clips |
|
Autonomous Docking (AVI, 22.5MB)
The clip shows the docking stratey. Vision is
initially used to find the docking station using a
camera. When the robot moves close enough to the
docking station, the laser rangefinder on the robot
scans for the laser beacon and determines its angle
to the wall. At a proper distance from the docking
station, the robot executes the blind docking
sequence based on the odometry.
|
|
Door Monitoring (AVI, 59.4MB)
The clip shows a robot performing a door-monitoring
task. The robot wanders while avoiding obstacles
until the main doors of the lab are detected, at
which time it stops and begins monitoring them.
Whenever someone opens a door, the robot takes a
picture every second the door is detected open
using a camera. Once the battery voltage level
reaches a preset lower limit, the robot begins the
docking sequence for recharging, and goes to
suspension mode until the battery is fully charged.
|
|
|
Acknowledgements |
This research was supported in part by DARPA under grant
DABT63-99-1-0015 and NSF under grant ANI-0082498. The first
author (Milo C. Silverman) was supported by a fellowship
from Raytheon Electronic Systems, Raytheon Company.
|
|
|
|
|
|